02/09/2022
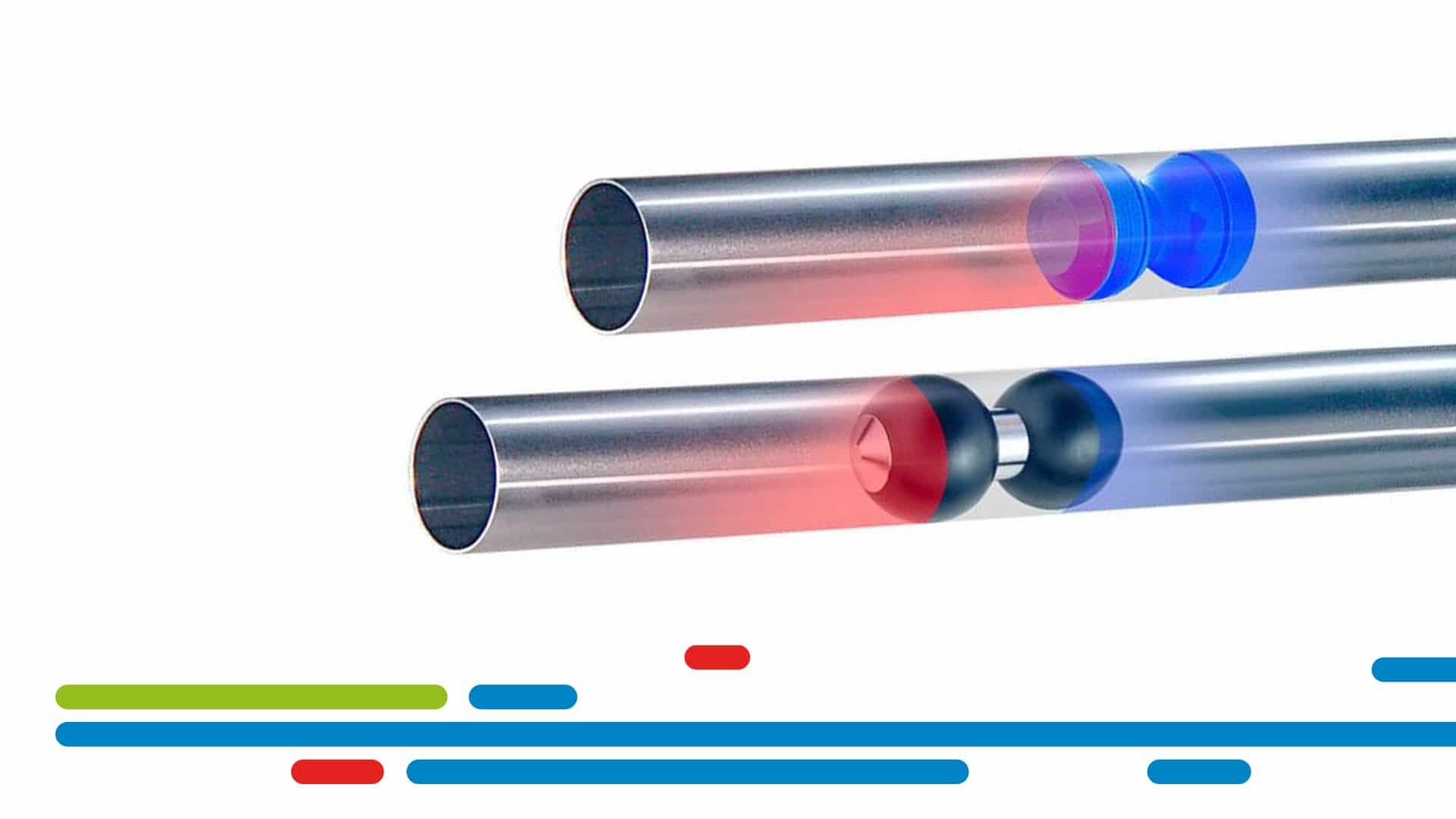
Pigging Case Study
The PROBLEM
However, cleaning between product changes is very time-consuming. Furthermore, there is a substantial product loss due to the large amount of end product still remaining in the pipes.
Do you have trouble cleaning your pipes or are you interested in what a product recovery system could mean for your process?
SKS supplies different types and brands of systems so we can always impartially calculate the best solution for your specific situation. After years of experience with pigging systems our engineers are convinced that he can demonstrate you his added value.
SOLUTION
In order to reduce product loss to a minimum and to reduce product change times as much as possible, our engineers soon came up with a product recovery system (pigging system).
By using this system, it is possible to recover virtually the entire contents of the pipes (in this case +/- 100 l). In addition, cleaning times are reduced considerably, since only a thin product film remains after pigging. If a pipe is filled completely with a viscous sauce, flushing the pipe will be very time-consuming and plenty of chemicals have to be used.
The greatest challenge was the filling machine’s buffer tank. Because of its limited buffering capacity, it was impossible to collect the entire contents of the pipes. By using low level and high level sensors on the buffer tank and constructing the pigging system in such a manner that pipes are emptied gradually, the end user can recover the entire contents of the pipes.
RESULT & CALCULATION
By using this solution, 16 to 18 tons of end product are “recovered” each year, an amount which was simply wasted in the present situation. With an average value of € 3 per kilo, this results in annual nett savings of € 48,000 up to € 54,000 per product.
Furthermore, the effective production time is approx. 1.5 to 2 times increased for each product change and the use of chemicals and energy is reduced.
All this was achieved With a total investment, including installation and automation, of € 50,000,- an amount which is recovered in 1 year, based on the above-mentioned data.
SKS! We know your process flow.